Ensaios Não Destrutivos
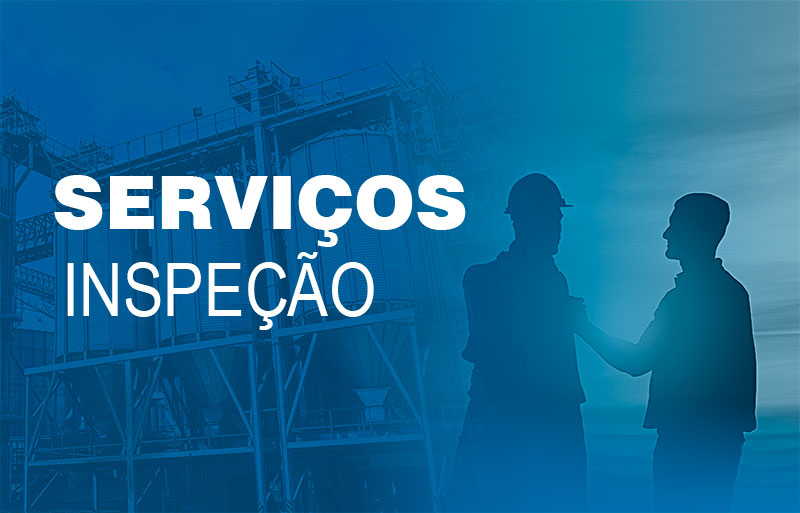
Ensaios não destrutivos (END) são técnicas para avaliar materiais e componentes sem causar danos, com o objetivo de detectar defeitos com precisão e garantir segurança e qualidade.
Descubra abaixo as soluções que oferecemos aos nossos clientes nessa área e como podemos ajudá-lo.
– Análise de Documentação
– Medição de Espessura
– Inspeção Visual
– Ensaio de Dureza em Campo
– Ensaio por Líquidos Penetrantes
– Ensaio por Partículas Magnéticas
– Ensaio Visual de Solda – EVS
– Inspeção Dimensional
– Ensaio por Ultrassom
– Ensaio Phased Array
– Ensaio Iris
– Ensaio Visual Remoto – Videoscopia
– Acompanhamento de Teste de Funcionamento
– Acompanhamento/Execução de Teste Hidrostático
– Medição de Rugosidade
– Medição de Espessura de Tinta
– Teste de Aderência de Pintura
– A/B-Scan
– C/D-Scan
Solicitar orçamento
Análise de Documentação
A análise de documentação é uma etapa muito importante no processo de inspeção, pois trata-se do início de tudo. É normal, antes de se executar qualquer inspeção, que se solicite a documentação pertinente ao item a ser inspecionado, seja ela de origem do fabricante/montador ou do fornecedor da matéria-prima ou do componente. No que tange inspeções de fabricação, normalmente são requeridos os certificados da qualidade de origem do produto (chapas, forjados, laminados, fundidos etc.), onde a checagem da sua rastreabilidade é imprescindível, e, também, os documentos gerados pelo setor de controle da qualidade do próprio fabricante, que, em tese, já teria que ter aprovado o produto a ser apresentado para inspeção externa.
Quando se trata de inspeções de montagem em campo, a avaliação da documentação também tem que ser inicialmente focada na rastreabilidade dos certificados apresentados, ou seja, de que forma os produtos em questão (tubos, curvas, conexões em geral, chapas etc.) são rastreáveis com os documentos apresentados. Obviamente, além disso, o seu conteúdo tem que ser avaliado para verificação da conformidade com normas técnicas pertinentes. Também, em campo, é comum a checagem da documentação referente aos processos de soldagem, onde se avalia a qualificação de soldadores, de procedimentos de soldagem e certificados de consumíveis.
Medição de Espessura
É uma técnica muito utilizada e facilmente executada devido à simplicidade de operação dos modernos equipamentos disponíveis no mercado. A medição de espessura é muito utilizada para verificar fenômenos de deterioração dos materiais como corrosão, abrasão, erosão ou mesmo suas combinações. É um ensaio simples, não intrusivo e com poucas limitações. Uma delas é a temperatura da superfície, que muitas vezes pode ser contornada com o emprego de transdutores apropriados e utilização de pastas de acoplamento adequadas a esta situação.
Este ensaio é largamente utilizado no monitoramento da perda de espessura das paredes de equipamentos sujeitos a pressão, o que permite controlar a sua vida útil remanescente.
Vale lembrar que a confiabilidade dos resultados sempre estará associada à execução dos serviços por técnicos treinados e capacitados e à utilização de aparelhos e padrões de calibração de boa qualidade e com aferição certificada.
Inspeção Visual
A inspeção visual é um evento de importância primordial e deve sempre preceder qualquer outra inspeção de um componente ou equipamento mecânico. Com ela se pode perceber rapidamente uma ausência de rastreabilidade na identificação de um componente, um mau acabamento de usinagem, um reparo de solda que não poderia ter sido feito, presença de trincas, irregularidades em corpos-de-prova apensos em peças fundidas, problemas causados pelo manuseio e estocagem da peça, desvios dimensionais grosseiros, condições de limpeza não adequada para realização de outras inspeções, condições inadequadas de pinturas ou outros acabamentos superficiais, estado de embalagens, além de várias outras situações. Um cenário em que é muito empregada é na inspeção de soldas durante a fabricação de equipamentos caldeirados. Desta forma, a inspeção visual é uma inspeção que sistematicamente deveria ser feita pelo inspetor em qualquer etapa de fabricação, montagem ou manutenção preventiva/corretiva de equipamentos ou componentes mecânicos.
Ensaio de Dureza em Campo
O ensaio de dureza em campo é uma inspeção rápida, útil, versátil e precisa. Os tipos de ensaios aplicáveis variam de acordo com a dureza do material a ser inspecionado, sua geometria e condições de acesso. Os tipos de ensaios de dureza por penetração comumente empregados em componentes mecânicos, principalmente metálicos, são: Brinell, Rockwell e Vickers. Outros tipos de dureza por penetração e outros tipos de ensaios, por exemplo, por rebote, também são empregados.
Uma grande vantagem deste ensaio, que é não destrutivo, é permitir que através do conhecimento da dureza do material se possa estimar a sua resistência mecânica à tração. Isso é muito usado, por exemplo, na caracterização de materiais utilizados na fabricação de vasos de pressão quando não se tem informações sobre eles, facilitando o cálculo e a verificação das condições de uso do equipamento e seu atendimento à NR13.
Ensaio por Líquidos Penetrantes
Este ensaio não destrutivo, pela sua baixa complexidade de execução, é um dos mais utilizados na detecção de trincas em componentes mecânicos e de porosidade em soldas ou materiais fundidos.
O ensaio por líquidos penetrantes baseia-se na aplicação e penetração de líquidos de baixa tensão superficial em superfícies onde se deseja avaliar uma eventual presença de trinca ou outras não conformidades, por ação do fenômeno da capilaridade. Posteriormente, após limpeza do excesso do líquido penetrante, é aplicado um revelador que absorve e traz para a superfície o líquido que penetrou na descontinuidade, tornando-o visível. Portanto, a inspeção por LP é aplicada para verificação de trincas superficiais difíceis de serem observadas a olho nu. Esta inspeção é muito utilizada na avaliação de soldas (raiz e acabamento) e em materiais não magnetizáveis, já que estes não permitem a realização do ensaio por partículas magnéticas. Por este motivo este ensaio é frequentemente aplicado na detecção de trincas em aços inox austeníticos (ex. AISI 304, AISI 316). Outro campo com ampla aplicação desse ensaio é na manutenção preventiva dentro das indústrias, com atenção especial na inspeção de vasos de pressão (região das soldas) para enquadramento na NR13.
Ensaio por Partículas Magnéticas
A inspeção por partículas magnéticas é um ensaio não destrutivo utilizado para detectar descontinuidades em materiais magnetizáveis, através do qual é possível visualizar defeitos superficiais e, em alguns casos, subsuperficiais. Apresenta características como simplicidade no princípio, facilidade de aplicação, liberdade de restrições quanto a tamanho, forma, composição e tratamento térmico dos materiais inspecionados, com a ressalva de que devem ser magnéticos.
A técnica consiste na magnetização das partes da peça (ou dela toda), aplicando-se logo em seguida partículas magnéticas (óxido de ferro) na forma de pó ou, normalmente, em suspensão em querosene ou em líquido de baixa tensão superficial (água misturada com distensor). Se o corpo apresentar alguma descontinuidade superficial a corrente elétrica forçará a passagem do campo magnético para fora do corpo, formando um campo de fuga que irá atrair as partículas magnéticas sobre a descontinuidade. Essas partículas se aglomeram e formam uma indicação visível da localização e da extensão do defeito.
Esse ensaio é muito aplicado durante a manutenção preventiva de equipamentos e componentes para detecção de trincas de fadiga de material. Também é largamente aplicado durante a fabricação de peças fundidas, já que estas normalmente podem apresentar trincas de solidificação ou mesmo reparos por soldagem. Na área de equipamentos caldeirados e tubulações, principalmente aqueles sujeitos a pressão, sua aplicação é normalmente direcionada para as regiões soldadas. Quando se trata da soldagem de aços baixa-liga, que exigem maiores cuidados e envolvem controles de pré e pós-aquecimentos, sua aplicação posterior é imprescindível.
Ensaio Visual de Solda - EVS
É o ensaio mais conhecido e utilizado dentre os métodos de END aplicáveis, sendo utilizado em fábricas, canteiro de obras ou indústrias em geral, podendo ser realizado pelo inspetor de solda – para soldas de fabricação – ou inspetor de equipamentos, nas inspeções de caldeiras, vasos, tanques ou tubulações.
Inspeção Dimensional
A inspeção dimensional é uma atividade realizada sistematicamente em várias etapas do ciclo produtivo de um equipamento ou componente para verificar a sua conformidade com o projeto, no qual, seguramente, sempre deverão constar tolerâncias e normas de referência. A aplicação da inspeção dimensional, por exemplo, permite evitar situações de reprova que seriam percebidas apenas quando o equipamento já estivesse pronto, o que pode reduzir custos e perda de tempo. Verificação da conformidade com os projetos construtivos, apertos e folgas de montagens, adequações de bases civis, medições de arqueamentos de tanques de armazenamento de combustíveis são alguns exemplos que podemos citar sobre sua grande utilidade. Para realização desta inspeção pode-se utilizar uma gama enorme de instrumentos de medição (paquímetros, micrômetros, goniômetros, trenas, réguas, prumos etc.), ou mesmo equipamentos ultrassônicos, como medidores de espessura.
Ensaio por Ultrassom
O princípio da inspeção por ultrassom baseia-se no fenômeno de reflexão de ondas acústicas quando encontram obstáculos à sua propagação dentro do material. A onda será refletida e retornará até a sua fonte geradora, isto se o obstáculo estiver numa posição normal (perpendicular) em relação ao feixe sônico emitido.
O ultrassom é o método de ensaio não destrutivo mais utilizado mundialmente para verificação de descontinuidades internas nos materiais. Geralmente, as dimensões reais de uma descontinuidade interna podem ser estimadas com uma razoável precisão através da altura dos ecos refletidos, fornecendo meios para que a peça possa ser aceita ou rejeitada, com base nos critérios de aceitação da norma aplicável.
As maiores aplicações desse ensaio estão relacionadas à inspeção de fabricação de peças fundidas, forjadas, laminadas, caldeiradas, medições de espessura, além da detecção e medição de profundidade de trincas, estas relacionadas à inspeção preventiva de componentes em uso. Outra grande utilidade é o seu emprego na inspeção de soldas de tubulações de vapor realizadas em campo como substituição ao ensaio radiográfico, evitando-se a necessidade de evacuar a área de trabalho para proteção da emissão de raios x, o que acaba por interferir nos cronogramas das obras.
A sua aplicação é extremamente necessária, por exemplo, na detecção de trincas em eixos de moenda quando montados em camisas que não vão ser sacadas durante as paradas. Com essa técnica, é possível varrer a região do eixo que está inacessível devido à camisa montada, para verificar a presença de trincas nessa área.
Por outro lado, existem algumas limitações para esse ensaio, como por exemplo, não poder ser empregado em peças fabricadas com materiais de alta atenuação acústica, como ferro fundido cinzento, metais não ferrosos (ex.: bronze), aços com microestrutura grosseira (sem tratamento térmico), etc. Peças de geometria complexa dificultam a realização do ensaio, já que a técnica requer que a região a ser varrida tenha superfícies paralelas. Altas temperaturas também dificultam a sua aplicação, assim como o acabamento superficial também é um fator limitante, já que a alta rugosidade superficial devido a riscos ou corrosão não permite a perfeita acomodação do transdutor (cabeçote) na superfície, o que afeta a emissão das ondas ultrassônicas pelo mesmo e acaba por comprometer o ensaio.
Ensaio Phased Array
Os métodos de inspeção por ensaios não destrutivos (END) são utilizados nos diversos ramos da indústria. A técnica de END por ultrassom é muito usada devido a sua alta confiabilidade, praticidade, baixo custo e também riscos desprezíveis para o operador e meio ambiente. Dentre as tecnologias de equipamento de inspeção por ultrassom, a Phased Array é a mais recente.O principal objetivo da técnica é detectar descontinuidades internas existentes nos materiais em diferentes tipos ou formas, com a finalidade de garantir a qualidade e diminuir o grau de incerteza na utilização de materiais para aplicações industriais.
Ensaio IRIS
O IRIS (Internal Rotary Inspection System) é uma técnica de teste não destrutivo (NDT) utilizada para inspecionar as superfícies internas de tubos e dutos. A técnica envolve a inserção de um transdutor ultrassônico rotativo dentro do tubo, que gera ondas sonoras que viajam pelo material e refletem de volta para o transdutor. A partir das informações coletadas, é possível gerar imagens detalhadas da parede interna do tubo, incluindo identificação de defeitos como corrosão, erosão e desgaste. O IRIS é uma técnica altamente precisa e confiável, sendo amplamente utilizada em indústrias como petróleo e gás, química, alimentícia e de energia. É uma técnica não invasiva que permite a inspeção de tubos sem a necessidade de removê-los do local, reduzindo custos e aumentando a eficiência na manutenção e monitoramento de tubulações
Ensaio Visual Remoto – Videoscopia
A videoscopia é uma técnica de inspeção visual realizada com câmera de vídeo onde não é possível se ter o acesso visual direto. Essa técnica permite observar, fotografar, filmar e, consequentemente, emitir relatórios com registros fotográficos ou vídeos. Permite ao técnico de inspeção tomar decisões sobre as condições operacionais do equipamento sem a necessidade de abrí-lo para se ter o acesso visual direto, economizando tempo e viabilizando análises de equipamentos em uso durante pequenas paradas programadas.
Oportunas aplicações dessa técnica estão relacionadas à avaliação do interior de equipamentos, sem a sua abertura, como, por exemplo, de engrenagens e pinhões de redutores, rotores de turbinas, entupimentos e incrustações no interior de tubos, dentre várias outras.
Acompanhamento de Teste de Funcionamento
Nas inspeções realizadas pela Welding os testes de funcionamento normalmente estão relacionados à fabricação de redutores de velocidade. Tais testes são realizados pelo fabricante sob o testemunho da Welding. Neles os equipamentos são montados em uma bancada de testes e colocados para funcionar (quase sempre) em rotação similar à de trabalho, aguardando-se uma estabilização da temperatura no mesmo. Normalmente se checam a pressão e temperatura do óleo do sistema de lubrificação, a temperatura dos mancais, a vibração axial, horizontal e vertical em todos os mancais e a intensidade do ruído. Tais parâmetros são comparados com as especificações técnicas do fabricante e, se compatíveis, os equipamentos são liberados para embalagem e expedição.
Acompanhamento/Execução de Teste Hidrostático
O teste hidrostático é comumente realizado na etapa de fabricação de vasos de pressão e caldeiras, como também pode ser solicitado pelo PH após a realização de algum reparo ou modificação no equipamento. A Welding elabora procedimentos de execução do teste e realiza o acompanhamento em campo do teste hidrostático.
Medição de Rugosidade
Toda superfície, por mais polida que esteja, possui imperfeições que podem estar acima do máximo definido em projeto. A Welding, através de um rugosímetro portátil, realiza a medição da rugosidade superficial do seu equipamento de forma rápida e eficaz.
Medição de Espessura de Tinta
Com o objetivo de verificar a conformidade da espessura de camada de tinta especificada pelo fabricante, utilizamos equipamentos medidores de espessura por ultrassom para verificação da espessura real aplicada.
Teste de Aderência de Pintura
Para avaliação da aderência da camada ou das camadas de tinta, dispomos do kit completo para preparação do ensaio em campo e teste com fita adesiva.
B-Scan
O ensaio B-scan é uma técnica por ultrassom destinada à avaliação da integridade da espessura de peças, chapas, tubulações, entre outros materiais. É conduzido com um aparelho de medição de espessura equipado com a função B-scan. Ao contrário dos aparelhos de medição de espessura convencionais, que possuem um mostrador alfanumérico e realizam inspeções por pontos, o B-scan realiza uma varredura e o gráfico resultante exibido na tela do aparelho proporciona uma visão em corte, permitindo ao operador identificar possíveis descontinuidades internas e analisar uma eventual perda de espessura.
Esse ensaio é amplamente empregado na avaliação de corrosão interna em equipamentos, vasos de pressão, tubulações, entre outros. Pode ser executado de forma automatizada, semi-automatizada ou manual, sendo que alguns aparelhos são capazes de gerar um registro do gráfico da inspeção.
C-Scan
O ensaio C-scan é uma técnica de ensaio por ultrassom desenvolvida para análise da integridade da espessura de materiais, como peças, vasos de pressão, tubulações, tanques, chaminés, etc. Ele é realizado utilizando um equipamento de ultrassom Phased Array (com múltiplos cristais) ou um sistema com softwares especiais. Sua visualização na tela apresenta uma imagem de planta (vista de cima), formando uma representação tridimensional da descontinuidade, fornecendo localização e tamanho.
O C-scan pode ser utilizado de forma automatizada ou semi-automatizada, com a vantagem de gerar um registro das imagens da inspeção. Trata-se de uma vista muito importante para a análise de descontinuidades no ensaio por Phased Array, que inclui outras vistas, como A-scan, B-scan e S-scan, entre outras.